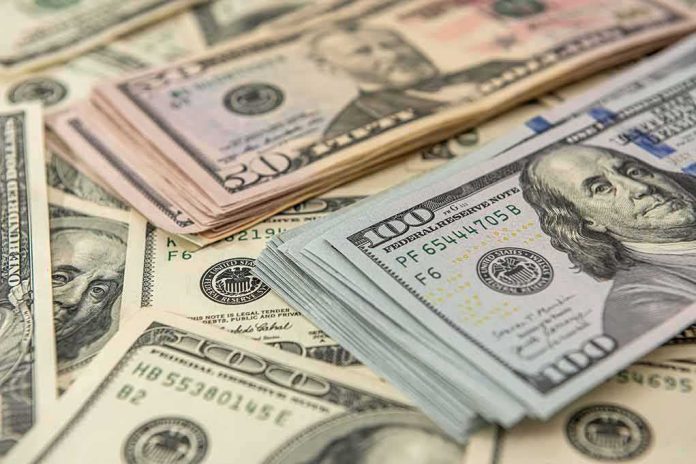
Home Depot’s massive $5.5 billion acquisition of GMS Inc. signals the end of America’s cheap labor era as major corporations embrace automation to counter workforce shortages.
Key Takeaways
- Home Depot is investing $5.5 billion to acquire GMS Inc., following its previous $18 billion purchase of SRS Distribution, marking a decisive shift away from reliance on low-skilled labor.
- The acquisition will integrate GMS’s 300+ distribution centers with SRS’s national footprint, giving Home Depot control over 1,200 locations and 8,000 trucks.
- This strategic move responds to reduced immigration under President Trump’s policies and growing opposition to mass immigration, forcing companies to prioritize automation and supply chain innovation.
- The deal represents a broader trend in American business toward domestic supplier consolidation and vertical integration in response to U.S.-China trade tensions.
- Wall Street analysts may misinterpret these consolidation deals as antitrust issues, missing the underlying driver of labor scarcity.
The End of Cheap Labor in America
Home Depot’s strategic $5.5 billion acquisition of GMS Inc. represents more than just corporate expansion—it signals a fundamental paradigm shift in how major American corporations are planning for a future where labor is increasingly scarce and expensive. This move, combined with Home Depot’s earlier $18 billion purchase of SRS Distribution, demonstrates a deliberate pivot away from business models dependent on abundant low-skilled workers. Instead, the home improvement giant is investing heavily in automation, sophisticated distribution systems, and supply chain dominance to maintain competitive advantage in a transforming labor market.
“The golden age for employers is coming to an end,” said Adrian Wooldridge.
The era when businesses could assume an unlimited supply of low-skilled labor is rapidly concluding. President Trump’s immigration policies have significantly reduced the influx of foreign workers, while public sentiment has shifted decisively against mass immigration. These changes have forced forward-thinking companies to reimagine their operations. Rather than lobbying for expanded visa programs, businesses are now investing in domestic infrastructure, sponsoring apprenticeship programs, and developing advanced technologies to reduce labor dependency. Home Depot’s acquisition strategy exemplifies this new approach.
Building Supply Chain Dominance
By acquiring GMS Inc., Home Depot is dramatically expanding its business-to-business supply chain capabilities for building contractors. GMS operates approximately 320 distribution centers specializing in drywall, framing, and tool services—a perfect complement to Home Depot’s existing retail operations. The integration of these facilities with SRS Distribution’s national footprint will give Home Depot unprecedented control over approximately 1,200 locations and a fleet of 8,000 trucks, creating a logistics network of extraordinary scale and efficiency.
This massive consolidation represents a capital-intensive business model with higher margins and significantly lower labor requirements than traditional retail operations. By focusing on volume, efficiency, and resilience, Home Depot is positioning itself to thrive in an environment where traditional labor markets can no longer be relied upon. The broader trend across construction and logistics sectors is toward automation and centralization of operations, minimizing labor touchpoints wherever possible while maximizing supply chain control.
Domestic Production and Trade War Strategy
Home Depot’s $110-per-share offer for GMS—which outbid QXO’s $5 billion proposal—underscores the company’s determination to dominate the contractor market. This aggressive acquisition also reflects a strategic response to ongoing U.S.-China trade tensions, which have increased tariffs on Chinese building materials and driven up costs for imported construction supplies. By consolidating domestic suppliers, Home Depot is reducing its vulnerability to international supply chain disruptions while simultaneously decreasing reliance on foreign materials.
The macroeconomic factors influencing this shift extend beyond labor considerations. President Trump’s tariff policies have encouraged domestic investment and production, creating an environment where vertical integration and control over supply chains provide significant competitive advantages. Investors are increasingly recognizing the value of companies with strong domestic production capabilities for critical materials and contractor-focused business models. The capital-intensive nature of reshoring operations favors larger firms with robust financial resources—precisely the position Home Depot now occupies.
The Future of American Business
The Home Depot-GMS deal exemplifies how forward-looking corporations are adapting to a labor-scarce, limited-immigration environment where scale and efficiency are paramount. Rather than fighting against demographic and political realities, these companies are embracing technological solutions and strategic consolidation. This represents a reversal from past models of importing workers to meet labor needs, instead encouraging the rebuilding of domestic labor supply chains through training, education, and automation.
Wall Street analysts may misinterpret these consolidation moves as merely antitrust concerns, failing to recognize the underlying driver of labor scarcity. However, the strategic importance of these acquisitions goes far beyond traditional market share considerations. Companies like Home Depot are building supply chain resilience amid geopolitical uncertainties, investing in automation to counter workforce challenges, and positioning themselves for sustained competitive advantage in a fundamentally changed business landscape. This strategic realignment will likely define American business evolution for decades to come.